In this article, you will learn the different types of paper tubes. These include Corrosion-inhibiting grade or VCI paper tube, Spiral and convolute tube manufacturing, Sealants, and End caps. Moreover, you will learn about the different applications of paper tubes. You will also discover how these tubes are manufactured.
Corrosion-inhibiting grade or VCI paper tube
Corrosion-inhibiting grade (VCI) paper is heavy packaging paper that is infused with a substance that protects against rust. It is used to wrap and protect metal parts and is resistant to rust because it does not absorb grease or oil from metal items.
Corrosion-inhibiting paper is available in many different forms, including tubes and 2D pouches. Corrosion-inhibiting grade (VCI) paper is made with proprietary chemistry, preventing corrosion on metals for years to come. It is a cost-effective solution for shipping products and prevents metal parts from becoming rusted and corroded.
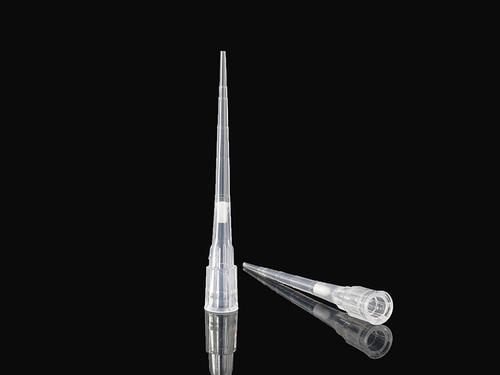
VCI packaging paper can be used to wrap or drape metal parts. The VCI molecules align on the metal surface to a depth of three to five molecules, creating a barrier against oxidation and preventing a corrosion cell from forming. Packaging material made from VCI has several advantages, and one of the main advantages is that it does not need to be air-tight. The protective layer is dissipated when the product is unwrapped. When the parts are unwrapped, the metal surfaces are clean. No washing or corrosion removal is necessary.
It is made of neutral kraft and contains vapor phase corrosion inhibitors that are effective against SO2s and galvanic corrosion between dissimilar metals.
Spiral and convolute tube manufacturing processes
Paper tubes can be produced in several different shapes and sizes. Both spiral and convolute tubes can be customized to meet the customer's specific needs. In addition to standard sizes, these tubes can also be customized with different colors and printings. Manufacturers can also offer customized labeling options that range from simple sticker-type labels to elaborate coding. These tubes can also be used for pyrotechnic applications.
Spiral tubes are created from a paper roll that is usually four inches wide. The paper is then wound at a specific angle around a mandrel. The mandrel's size determines the inner diameter of the core. When the core is finished, a blade cuts it into the desired diameters.
Convoluted tubes, on the other hand, are made from multiple plys of paper. They can be made from one or more sheets of paperboard or brown kraft paper. They can also be wrapped in specialized paper that provides specific characteristics, such as water resistance or a particular color. Both spiral and convolute paper tubes are used for packaging.
End caps
End caps for paper tubes are a great way to protect your mail and other packages from breakage and damage. They fit tightly around the mailing tube and are tough enough to handle the rigors of shipping and handling. These caplets also provide a secure closure and can be reused countless times.
These caps protect the ends of a paper tube by preventing it from rolling and tearing. They also add a professional finish to the product, enhancing its durability and increasing its aesthetic appeal. Plastic end caps are available in various polymer grades, which vary depending on the weight that the tube can hold. They also come in a variety of sizes.
Caps are available in many different materials and can be used for a wide variety of applications. You can choose from silicone, EPDM, and vinyl caps. You can also choose from PVDF, polycarbonate, and nylon 66.
Sealants
Paper tube accessories include sealants, end caps, and plugs. They help protect paper tubes from damages caused by moisture, chemicals, and heat and cold. Plugs, on the other hand, help prevent contents from slipping out of the tubes. Sealants and end caps are also useful for keeping contents inside.
In order to select the best sealant for your tube, it is important to check its adhesion and strength. You can use ASTM C794 to determine the bond strength. However, the actual value may vary depending on the hardness of the sealant and the substrate. For most applications, a value of ASTM C920 is acceptable.
When selecting a sealant, consider the temperature of the surface. While some sealants are not suitable for high-temperature environments, those that are placed on the sunny side of a building can experience temperatures as high as 70degC (177degF). For these applications, a sealant should be chosen that is resistant to high temperatures. However, it is best to contact the manufacturer for further information regarding its heat and chemical resistance.